LEADERMAC | Platinum Moulder SeriesLEADERMAC | Platinum Moulder SeriesCookie and Privacy Settings
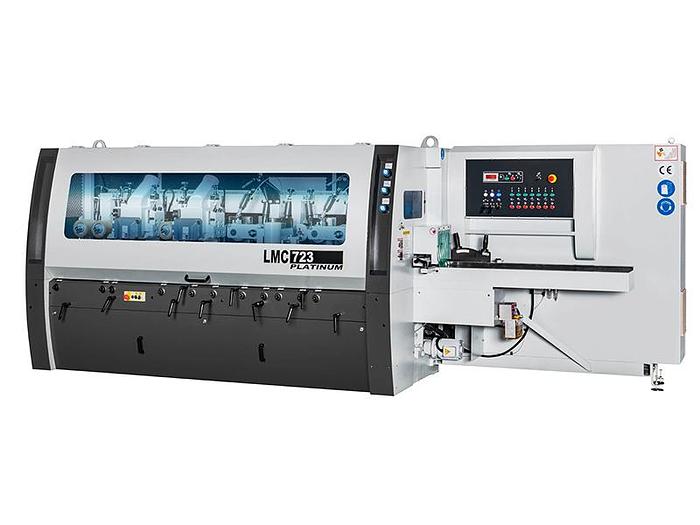
LEADERMAC | Platinum Moulder SeriesLEADERMAC | Platinum Moulder SeriesCookie and Privacy Settings
or
Call 239-770-4474
Description
Why Leadermac Platinum Moulder Series?
A full touch screen control system keeping all history files, downloads info from the grinding room, triple electronic position readouts for each axis, precision sets, troubleshooting, and more.
The programmable controller provides convenient thickness and width of cut settings, creating organization leading to rapid change-overs and more production.
Precision spindle assemblies including four high-precision bearings, each for the highest tolerances and superior finish results.
Industrial moulder design with a solid cast iron frame produces unparalleled finished part quality in its class.
The Platinum moulder comes with high-quality components, ensuring the best finish possible.
4 pieces of Abec 7 Precision Bearings per spindle – ensuring an excellent finish on your products.
8000 RPM spindles allow faster production to meet your needs.
The Platinum moulders design ensures easy and consistent set up by your operator, ensuring quick changeovers.
Turnkey solutions include on-site operator and maintenance training.
Heavy-duty cast iron frame provides superior vibration damping, which produces superiorly finished parts and promotes long bearing & machine life.
Tightly coupled machine ensures smooth and consistent feeding to assist in producing a high-quality finish.
All tables and fences hard chromed with approximately 0.012″-0014″ thick hard chrome, which ensures maximum longevity.
Comes with more top-driven and bottom full-width driven feed rolls than other moulders of its size.
8000 RPM spindles each with (4) ABEC 7 precision bearings per spindle which provides smooth surface finish results.
Pneumatic side holdover provides consistent side pressure to the fence.
Pneumatic hold down pressure to all top feed rolls provides consistent and repeatable pressure.
Pneumatic chip breakers ensuring consistent pressure.
Full width driven infeed & outfeed bed rolls.
Increased Axial adjustment to vertical spindles.
Short stock feed roll station.
Dual SIKO quick set counters to assist in quick and accurate changeovers (other setworks systems available to increase automation).
Axial adjustment of last bottom head from the front of the machine.
Automatic and programmable table lubrication system.
Centralized grease lubrication system.
Safety sound enclosure is standard.
Pneumatic pressure to chip breakers, holdovers, and top feed rolls.
Variable frequency drives for spindles: allow RPM of spindles to be varied and act as a fully electronic braking system.
Split hold down pressure shoe.
Anti-kickback fingers for ripping operations.
Rip bed plates / special pressure shoe for ripping operations.
Universal spindle.
7200 RPM spindles for increase feed speeds.
12″ or 13″ wide machines with outboard bearings.
Grooved bed machines for short part feeding.
Telescopic top feed roll unit opposite left vertical side head.
Easyset Setworks System with touch screen control, memory, and motorized positioning for near side and top head.
Smartset 100 Setworks System with touch screen control, memory system, and motorized positioning for near side and top head, utilizing ball screw and rotary encoder for true accurate and repeatable positioning.
Proset Setworks system, with link to the grinding room, allowing the building of tool, profile libraries. Transfer of measurements after grinding via a video measurement stand to the PC to update all profiles. This system is designed to ensure the fastest of changeovers, allowing easy management of larger numbers of tools, product profiles, and changeovers as required.
Router spindles for special profiling.
Automatic width setting with measuring probe for random width material.
Multiple ripsaw spindle with sleeve.
Vertical spindle slicing/ripping system.
Special requirements on request.
Specifications
Manufacturer | Leadermac |
Condition | New |